
FEATURES
Latest Carding machines are having all the latest system and control system to Run the Carding machines at best efficiency / good quality / low breakage / Better Sliver CV% and high production rate.
By installing Karom Upgradation Kit in Carding you will achieve those all benefits which you will get in the latest carding machines, but at the same time you will also get much more than the latest machines.
- 1). Input signals feed : Infeed count
- 2). Output signals : feed speed in the chute
- 3). Control unit for signal processing
- 4). Input signal : delivery speed
- 5).Output signal : feed roller speed
- 6). Countrol signal : light barrier
- 7). Input signal : silver count
What we change in carding in this Kit.
1) We change the FBK/DFK/CHUTE FEED Motor and Drive from DC drive to AC Servo Drive so to eliminate the problem of frequent variation of speed due to carbon brushes of DC and also to eliminate the drive problems like frequent failure of old drives and needed frequent adjustment in drives.
2) We change the FEED ROLLERS Motor and Drive from DC drive to AC Servo Drive so to eliminate the problem of frequent variation of speed due to carbon brushes of DC and also to eliminate the drive problems like frequent failure of old drives and needed frequent adjustment in drives.
3) We change the DOFFER Motor and Drive from DC drive to AC Servo Drive so to eliminate the problem of frequent variation of speed due to carbon brushes of DC and also to eliminate the drive problems like frequent failure of old drives and needed frequent adjustment in drives.
4) We change the COILER Motor and Drive from DC drive to AC Servo Drive so to eliminate the problem of frequent variation of speed due to carbon brushes of DC and also to eliminate the drive problems like frequent failure of old drives and needed frequent adjustment in drives.
5) We change the Information System and display from normal system to the latest Touch TFT Ethernet system. Which gives most of information just by one click.
6) We install the Quality Information System to give the quality data of output sliver in terms of CV% of 1/3/5/10/100 Meter and Running A%, and Thick places in outcome sliver, Spectrogram, Um%, Speeds and suggest Speeds Selection according to Run Material.
7) We install Autolevelling system in FBK/DFK/CHUTE FEED to deliver the feed to card in levelled manner to reduce CV%, Um% and even quality of sliver in terms of Neps.
8) We Modify Feeding Autolevelling in a manner so that the card gives best CV% of sliver.
9) We also Modify Autolevelling at Exit point and remove all problems which at present with existing system and the Carding gives uninterrupted continuous better CV%.
10) We also install PLC drive latest of Fuji Alpha 5 and remove all PCB which gives continuous trouble and failure.
11) We modify the Carding Sliver Tension draft according to atmosphere and running material to overcome the breakage problem. Artificial Intelligence.
12) We also Change the Mechanical parts which gives day to day problem and mill invest unnecessary money on those parts.
13) Mill can see all the parameters of quality information anywhere online.
14) Our system can be modified and repaired from long distance.
15) We install Monitoring of waste choking in Licker-In ducts and Back and Front Suction Hood Ducts to give feedback to mills for waste deposition to overcome quality issues due to choking.
16) We install Maintenance schedule in Carding and it always display Grinding and changing schedule on Screen. It also sent mail to the responsible person that the activity is coming or overdue.
17) We have Thick Place monitoring and mill can stop the card as per there acceptance of thick places. Mill can see Thick places size, length and no of thick places in 10 meters.
18) We also install maintenance Program speeds to do work during Maintenance and Wire maintenance like grinding, mounting, speed check, reversing etc…
BENEFITS:
i) No expenditures on PCB/Drive repair/replacements, very easy maintenance only cleaning.
ii) Power savings which is from 15-25% lesser.
iii) 70% lesser CV% of 3 meter Cv%.
iv) Continuous correction of material, no choking.
v) Better quality in terms of Neps and also better yarn results.
vi) Thick Place measurement and monitoring with data recording.
vii) Maintenance Schedule and warning to keep the quality constant.
viii) Online monitoring of quality parameter with stop control.
ix) One touch information system.
x) Better Um% and card can be stopped by mill as per requirement of Um%.
xi) Online Spectrogram to analyse the mechanical problems of parts.
xii) Levelling Intensity for (N-1) & (N+1) A% correction.
xiii) Slow Speed Autolevelling Correction.
xiv) Superior Sliver Evenness at Higher Delivery speed by Alpha 5 Servo and Drive System.
xv) Remote access by Phone/Computer.
Auto Leveling in Carding:
In the spinning mill, the card is the effective part of the process, since the first intermediate product, the sliver, is produced here. A relatively high degree of evenness is required in this product. For various reasons, the card cannot always operate absolutely evenly, for example, owing to uneven material feed. Spinning mills are therefore forced to use auto leveling equipment under highly varying circumstances. Different principles for auto leveling can be selected depending upon the quality requirements and the operating conditions in the individual mill.
CLASSIFICATION OF AUTO LEVELING IN CARDING
- Short term auto leveling
- Medium term auto leveling
- Long term auto leveling
IRREGULARITIES CAN ACTUALLY BE COMPENSATED:
- In the material supply system.
- At the feed.
- At the delivery.
The material supply should operate with the greatest possible degree of accuracy in any case, since this has a direct effect on sliver evenness. The main regulating position is the feed; adjusting the feed roller speed, usually performs auto leveling. A distinction should also be drawn between:
- Short-term leveling systems, regulating lengths of product from 10 – 12 cm (rarely used in carding).
- Medium-term leveling systems, for lengths above about 3 m.
- Long-term leveling, for lengths above about 20 m (maintaining count). In addition, regulating can be performed by open-loop or closed-loop control systems
In addition, regulating can be performed by open-loop or closed-loop control systems .

Karom Auto leveling in the Chute:
Karom Chute leveling operates as Long-term leveling (Open-loop, produced by a proportional-integral regulator) and is performed by a microprocessor. In the feed to the chute the feed measuring device records the fluctuations in the Pressure fluctuation at four places. The speed of the feed roller of the chute is changed electronically so that these fluctuations in the Pressure are leveled out. However, the filling level is also used for regulating the feed rollers in the chute but is considered as an additional control parameter.

KAROM AUTO LEVELING IN THE IN FEED
Karom card leveling operates as medium-term to long-term leveling (closed-loop, produced by a proportional-integral regulator) and is performed by a microprocessor. In the feed of the card the feed measuring device records the fluctuations in the cross-section of the batt feed. The speed of the feed roller of the card is changed electronically so that these fluctuations in the cross-section are leveled out. The chute is also included in the control loop. However, the filling level is not used for regulating the feed rollers in the chute but is considered as an additional control parameter. In the delivery of the card a pair of disc rollers scans the cross-section of the carded sliver as it emerges. These readings are compared electronically with the preselected set value. Deviations in the set value are corrected electronically by altering the speed of the feed roller in the card.
Karom Auto leveling at Delivery:
Karom Card leveling at delivery operates as Short-term leveling (Closed-loop, produced by a proportional-integral regulator) and is performed by a microprocessor. In the feed of the card the feed measuring device records the fluctuations in the cross-section of the batt feed & at delivery the fluctuation in the cross section of the sliver measured by special sensor and the combination of both performed by a microprocessor. The speed of the feed roller of the card is changed electronically so that these fluctuations in the cross-section are leveled out. These readings are compared electronically with the preselected set value. Deviations in the set value are corrected electronically by altering the speed of the feed roller in the card.
ELECTRICAL FUNCTIONAL BLOCK DIAGRAM

AUTOLEVELLING SENSOR TEST REPORT
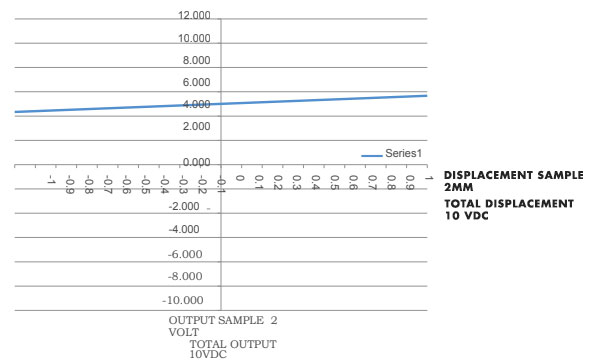
PROGRAMMABLE LOGIC CONTROLLER(PLC)
Programmable Logic Controllers (PLC) Operate according to user- programmed internal logic. Unlike office computer, PLC are degigned to be operated in industrial environments for the control and operation of manufacturing process equipment and machinery.
Input Unit:-
Monitors the change in status from an input derive connector to the PLC.
Output Unit:-
It generayes signals to be sent to an output device.
CPU Unit:-
It govems all plc activities. The primary function is to examine the status of nput, execute the program, and update the output. The cpu unit contains the memory section used to hold user program and data.
Programming Device:-
Enter and Monitor use program.
Power Supply:-
The power supply provides power to the CPU and the bus connection between each unit.
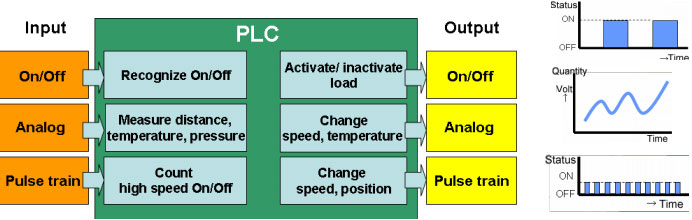
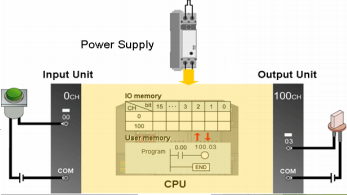
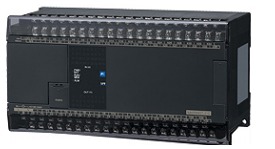
PROGRAMMABLE LOGIC CONTROLLER(PLC)
The slim and compact SX Series Support Digital Input/Output and is built in with multipleanalog input channels.
ADVANTAGES
- TR DO Point: 24
- DI Points: 36
- Communication Port: Built-in RS-232C and RS-485, compatible with Modbus ASSII/RTU communication protocol
- Built-in high speed counter
- High-Speed pules
MERITS OF OUR SYSTEM
- Expected 5 meter CV less than 1.5%
- Expected U% between 2% to 4%
- Electrical maintenance cost can be reduced by 20%
MACHINE REPLACEMENT
BEFORE | AFTER |
---|---|
FBK/DFK/CHUT — Motor and Drive![]() | ![]() |
Card FEED Roller — Motor and Drive![]() | ![]() |
Doffer — Motor and Drive![]() | ![]() |
Coiler — Motor and Drive![]() | ![]() |
Display![]() | ![]() |
Waste Duck Choking Monitoring System | ![]() |
Autoleveller | ![]() |
Quality Moniter | ![]() |
Control System![]() | ![]() |
Electric Panel![]() | ![]() |